Enhanced Durability: Geopolymer Concrete Amidst Acidic Environments
Enhanced Durability: Geopolymer Concrete Amidst Acidic Environments
By: Yoanna Suhartana
Concrete remains a fundamental material in the global construction industry, primarily due to its durability, strength, and versatility in being molded into various shapes. However, conventional concrete based on Ordinary Portland Cement (OPC) is notably vulnerable to aggressive environments, particularly acidic conditions. In such settings, the calcium compounds in OPC readily react to form new substances like gypsum, accelerating structural degradation. One promising alternative is geopolymer concrete, which can be synthesized from high-calcium fly ash (Class C), bamboo combustion residues, or kaolin. Numerous studies have demonstrated that geopolymer concrete (GPC) exhibits superior resistance to acid attacks while offering environmental benefits through reduced carbon emissions and the utilization of industrial waste.
One key advantage of geopolymer concrete lies in its more stable density compared to OPC-based concrete. According to Lavanya and Jegan (2015), fly ash-based geopolymer concrete experienced only a 2.5-4% decrease in density after immersion in sulphuric acid and magnesium sulphate solutions-significantly less than the up to 7% density loss recorded in OPC concrete. Density plays a crucial role in determining compressive strength and durability; denser concrete typically demonstrates enhanced strength and greater resistance to aggressive environments. High density also correlates with reduced porosity and permeability, enhancing the concrete’s resilience against water infiltration, chloride ions, and chemical attacks such as those from acids and sulphates.
Lavanya and Jegan’s research further confirmed that fly ash-based geopolymer concrete retains its compressive strength more effectively than conventional concrete when subjected to acid exposure. After 45 days of sulphuric acid exposure, geopolymer concrete exhibited only a 12-20% reduction in compressive strength, compared to a 28% reduction in OPC. In a separate study, geopolymer concrete made from bamboo ash and kaolin demonstrated merely a 4.5% strength loss over six weeks, whereas OPC concrete suffered a 23.8% reduction. These findings reinforce the mechanical reliability of geopolymer concrete in extreme conditions.
The exceptional performance of geopolymer concrete can be attributed to its unique chemical composition. Both Class C fly ash and bamboo-kaolin mixtures are rich in silica (SiO2) and alumina (Al2O3), which, when activated with alkaline solutions such as NaOH and Na2SiO3, form a dense and stable three-dimensional aluminosilicate network. Unlike the hydration products of cement that produce portlandite (Ca(OH)2) and calcium silicate hydrate (C-S-H), which are susceptible to sulphate attacks, geopolymer structures resist ion dissolution and the formation of destructive compounds like gypsum. In some instances, an amorphous silica layer forms on the surface, serving as an additional protective barrier against chemical attacks.
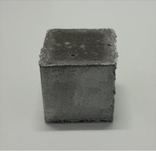
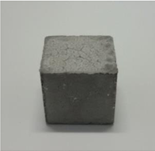
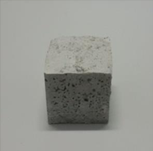
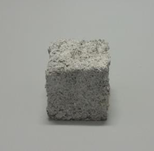
Despite its advantages, geopolymer concrete has yet to be widely adopted in the construction industry, primarily due to its relatively high production cost. Continued research is necessary to optimize production methods and reduce costs, thereby enabling geopolymer concrete to become a cost-effective and durable alternative to conventional materials in large-scale applications.
References
Lavanya, G., & Jegan, J. (2015). Durability Study on high calcium Fly Ash based geopolymer concrete. Advances in Materials Science and Engineering, 2015, 1–7. https://doi.org/10.1155/2015/731056
Purbasari, A., Samadhi, T. W., & Bindar, Y. (2018). Sulfuric Acid Resistance of Geopolymer Mortars from Co-combustion Residuals of Bamboo and Kaolin. ASEAN Journal of Chemical Engineering, 18(2), 22–30. https://doi.org/10.22146/ajche.49533